Custom Parts Development
Discover the Power of Custom
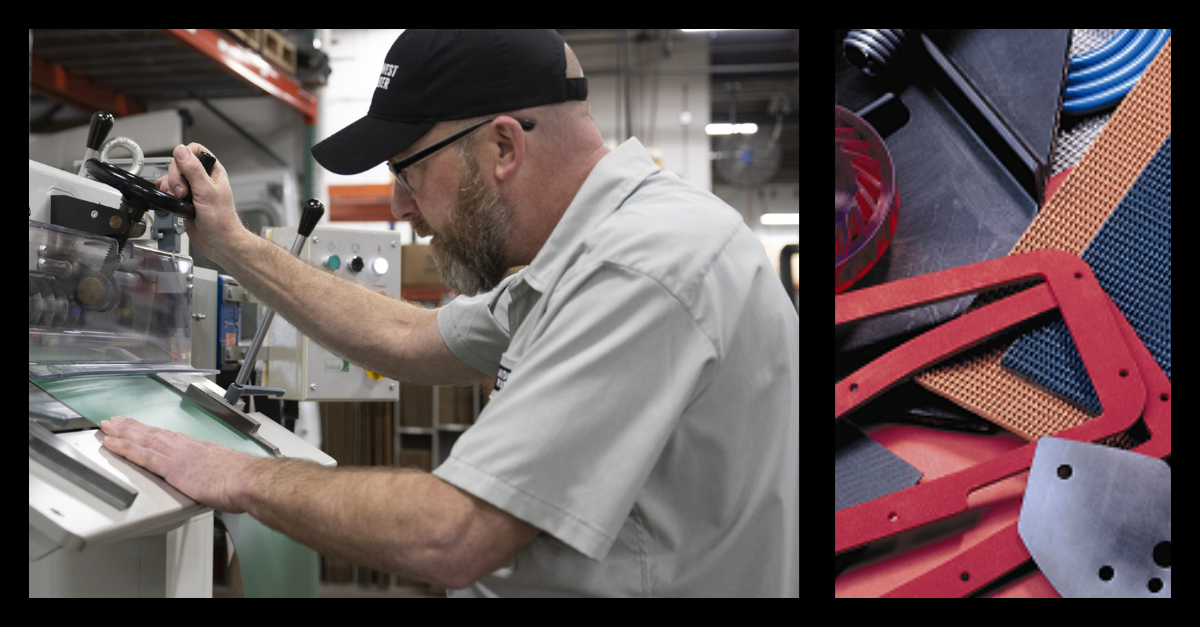
Break the Cycle
Say goodbye to off-the-shelf parts that wear out too soon, don’t perform, or cost too much.
Custom Parts, Simplified
Our straightforward process makes it easier than ever to get exactly what you need.
One-Time Setup, Long-Term Savings
Walk through our custom process once and streamline your reorder cycle for good.
Material Choices
We can help you choose right the first time. Two rubber parts from two different companies can look exactly the same yet their material formulation and corresponding properties can be very different. One works great the other one doesn’t. Rubber formulations are invisible, so our team is highly trained in material selection. We can narrow down the options so you can make the right choice.
Dense Products
Linatex
Pure Gum
SBR
Neoprene
EPDM
White Nitrile
Urethane
Silicone
Reinforced Silicone
Ci Sheeting
Cellular Products
EPDM Sponge
SBR Sponge
Silicone Sponge
Natural Sponge
Polyurethane Foam
Neoprene Sponge
Microcellular Urethane Sponge
Other Materials
XLPE – Cross Linked Polyethylene (Low Cost)
PVC / Nitrile Blend (Gaskets, Seals)
Polymide Materials (Insulation, Fire Resistent)
EVA – Ethylene Vinyl Acetate (Gaskets, Seals)
Silicone Foams
Custom Fabrication Capabilities
Fabrication Capabilities
Precision slit rubber and sponge
Custom laminations and perforations
Roller covering
Timing Belts & V-belts – Covered
Chute lining with rubber, plastic or Linatex
Vulcanizing
Sewing
Milling, drilling, turning or saw cutting of plastic or rubber
Sleeves
Rubber bonded to metal
Plastic: cut to size, drill, bevel, form/bend
Molding Capabilities
Dip molding
Injection molding
Extrusions
3D Printing
Compression molding
Thermoforming
Cutting Capability
Die cut
Hand-cut gaskets
Flash cut
Laser cut
CNC machining
Slitting
Research & Development
Design consultations
CAD drawings
Reverse engineering
Prototyping
Machine optimization testing
Leak testing
Other Capability
Kit assemblies
Part stamping
Special packaging
Labeling
Bar coding
Your Plant Isn't Generic. Why Are Your Parts?
When it comes to developing wear parts, there are so many material and fabrication options it's hard to know which combination will work best for your equipment. From design to distribution, Midwest Rubber will work with you to create a part that is the best balance of budget, performance and manufacturability.
Equipment manufacturers and processors call on Midwest Rubber as a development partner for help with unique challenges. We have earned their trust through our selection and knowledge of materials, experience in product design, research, development, testing capabilities, and extensive production facilities.
Our project managers work along side you thinking proactively and asking questions that lead to insights for improvement. We can help you find or create opportunities for improved cost savings, performance, manufacturability, or functionality. By involving us early in the process, you can meet your goals for development time and cost.
For years we have been mastering the art of material properties, design and fabrication to produce custom parts that last longer and deliver superior performance so you can focus on using your equipment not fixing it.
I appreciate Midwest Rubber's patience and willingness to listen and understand our specific application. We have been looking for something exactly like this for years"
Erik K.
Maintenance Manager
Getting the right part will save you time and money
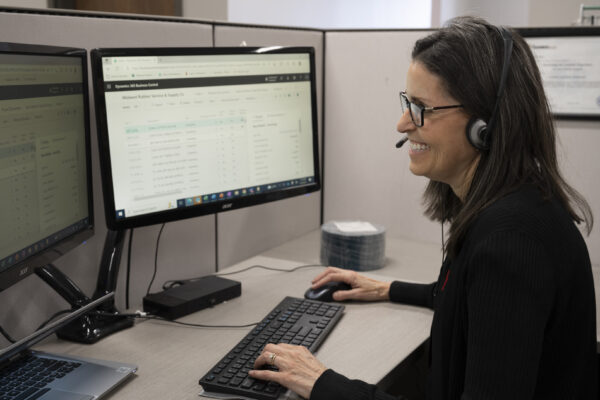
Co-Design the best part
We can present options that will increase performance, decrease cost, and improve durability
Prototype, sample and test
We can provide samples and prototypes fast, so you can test and make adjustments
Keep machine goals on target
From design to distribution we work along side you as an extension of the team to ensure your performance and budget goals are met